Large Sla Printer
SLA-800 3D Printer
- Print size: 800 (x) * 800 (y) * 400 (z) mm
- 0.025-0.3 mm print layer thickness and 85HM laser spot size
- SLA printed products are cured again by the secondary curing box,which can effectively improve the strength and toughness of the product
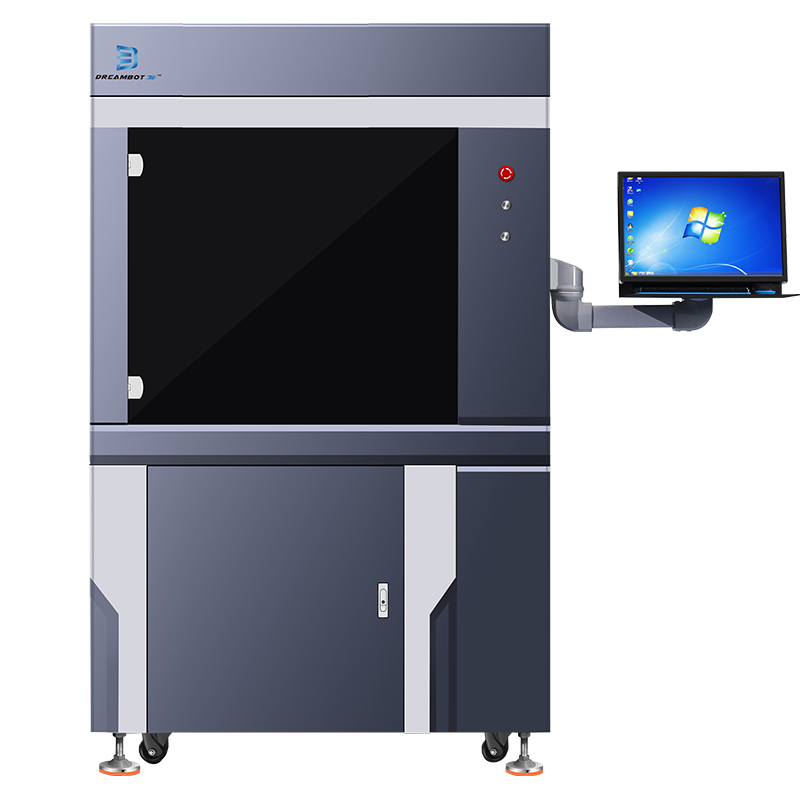
Dreambot3D Large Sla Printer
Dreambot3d Large Sla Printer machine utilizes galvanometer scanning technology for fast and accurate printing, with a layer thickness ranging from 0.025 to 0.3 mm.
SLA-800 3D printer emphasizes precision, efficiency, and high-quality results. It features a large industrial operating platform with a user-friendly interface, making it easy to use.
The printer is designed with a closed body to enhance success rates by blocking harmful particles. Its high-precision lead screw slide table and stable electrical system ensure reliable and consistent performance.
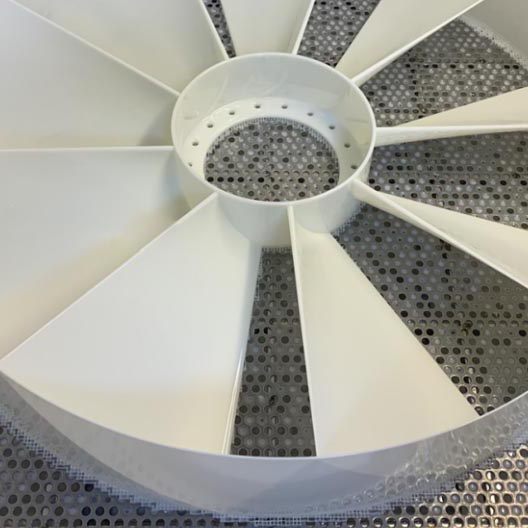
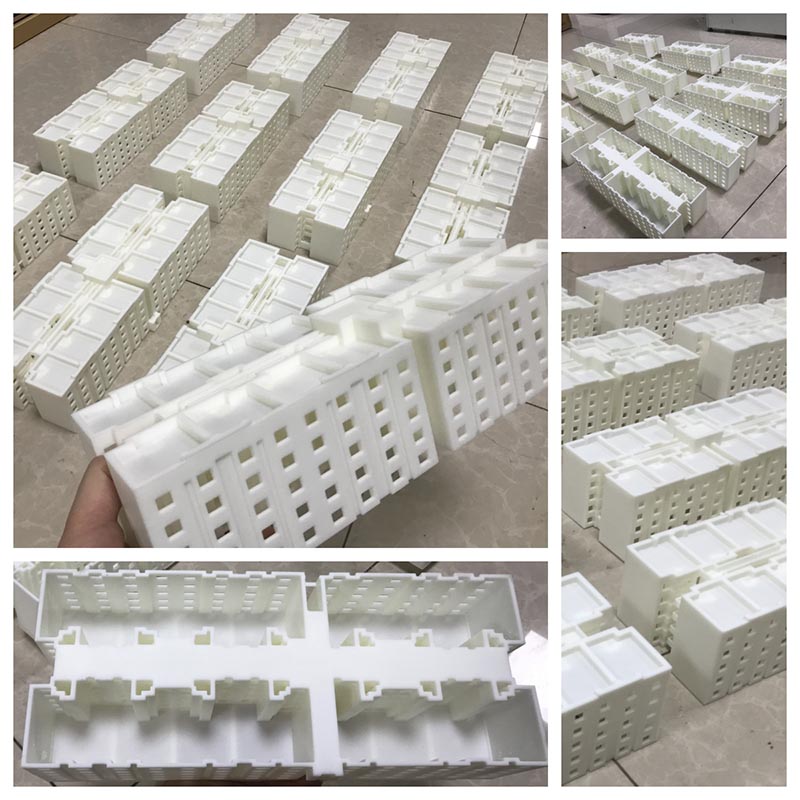
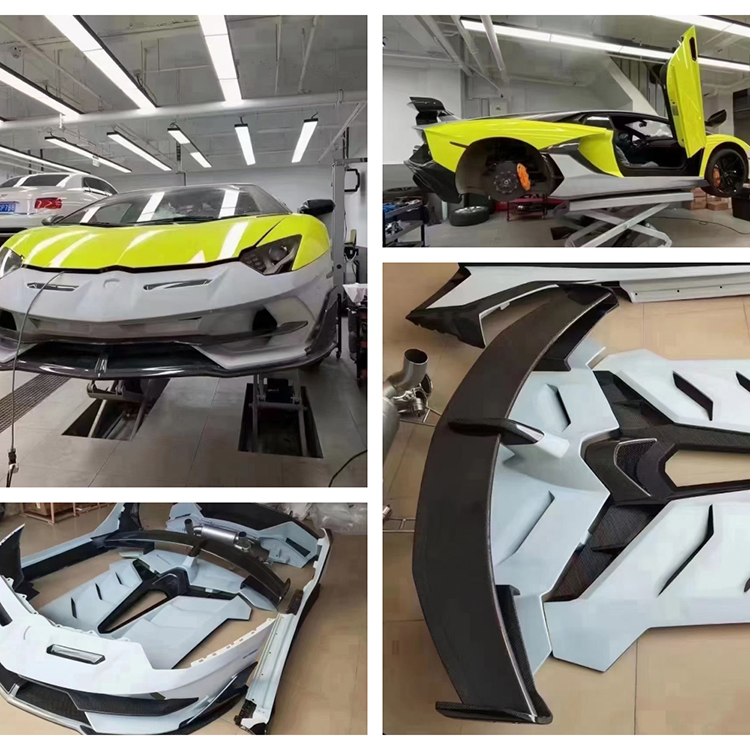
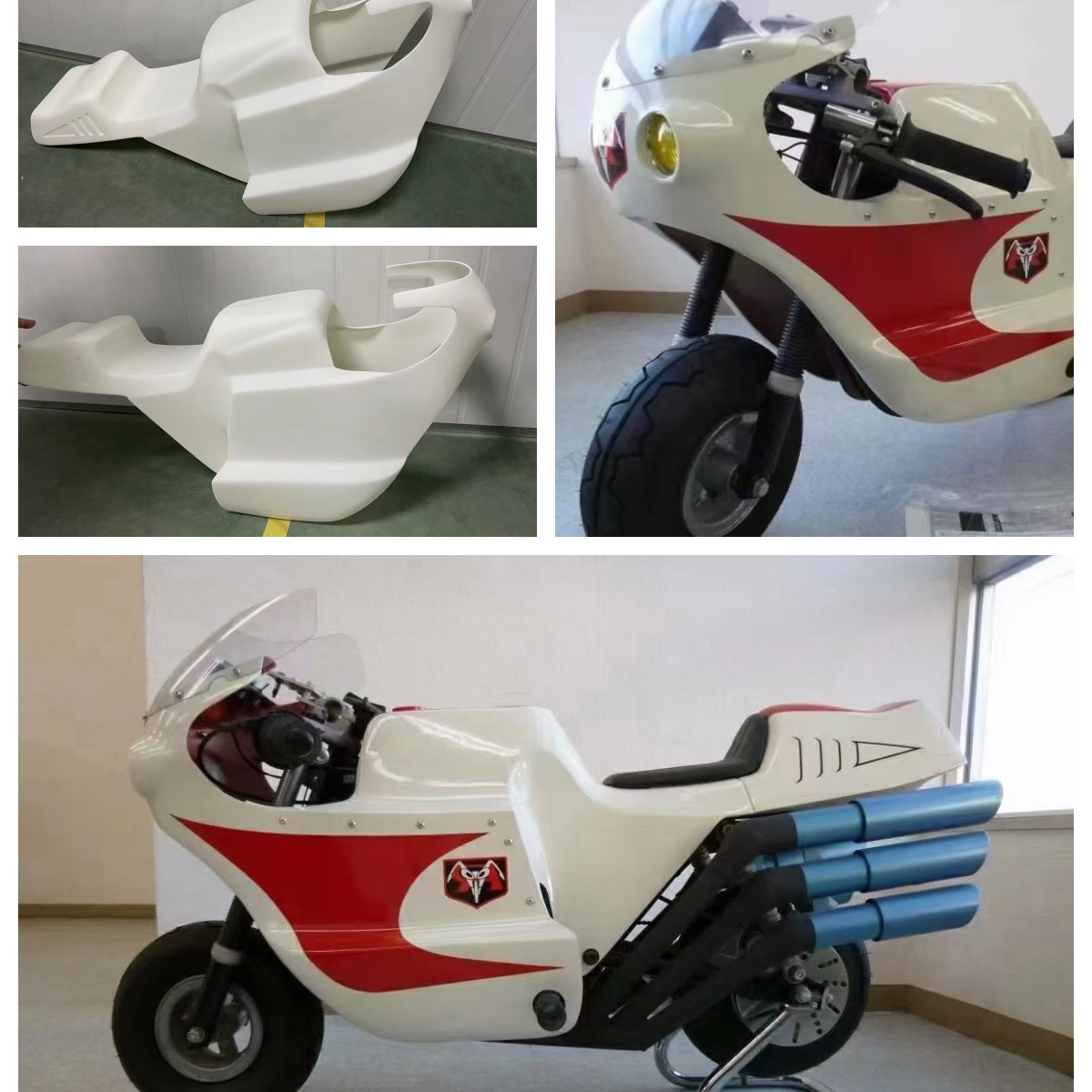
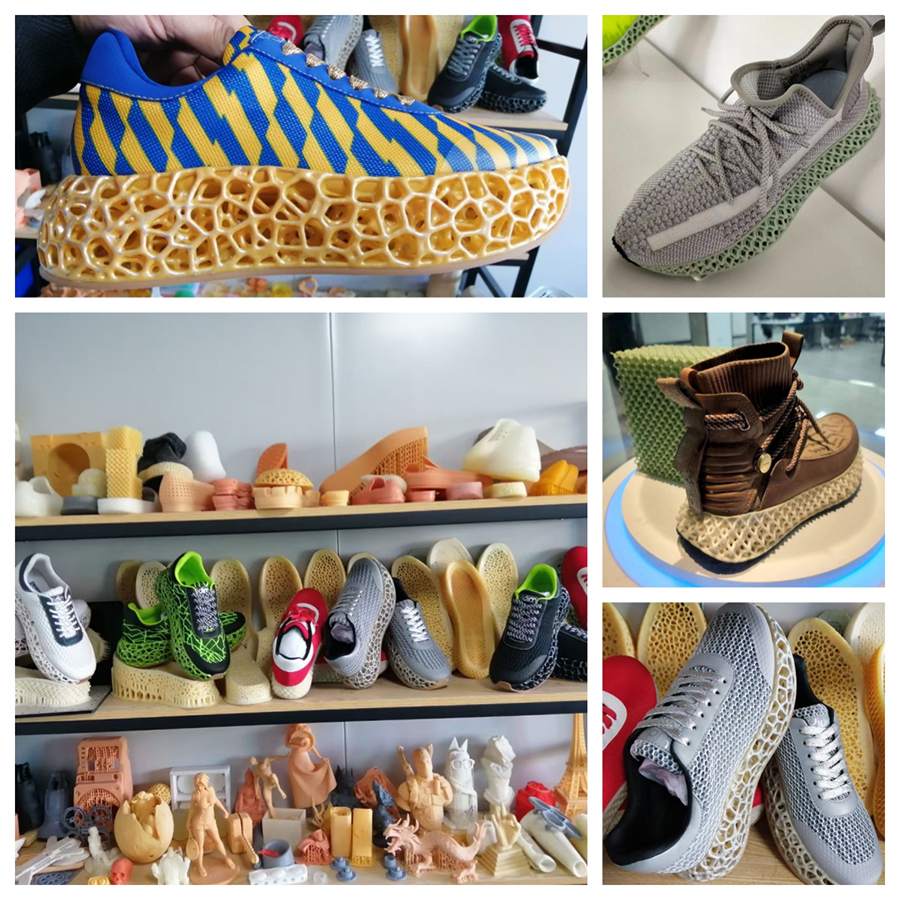
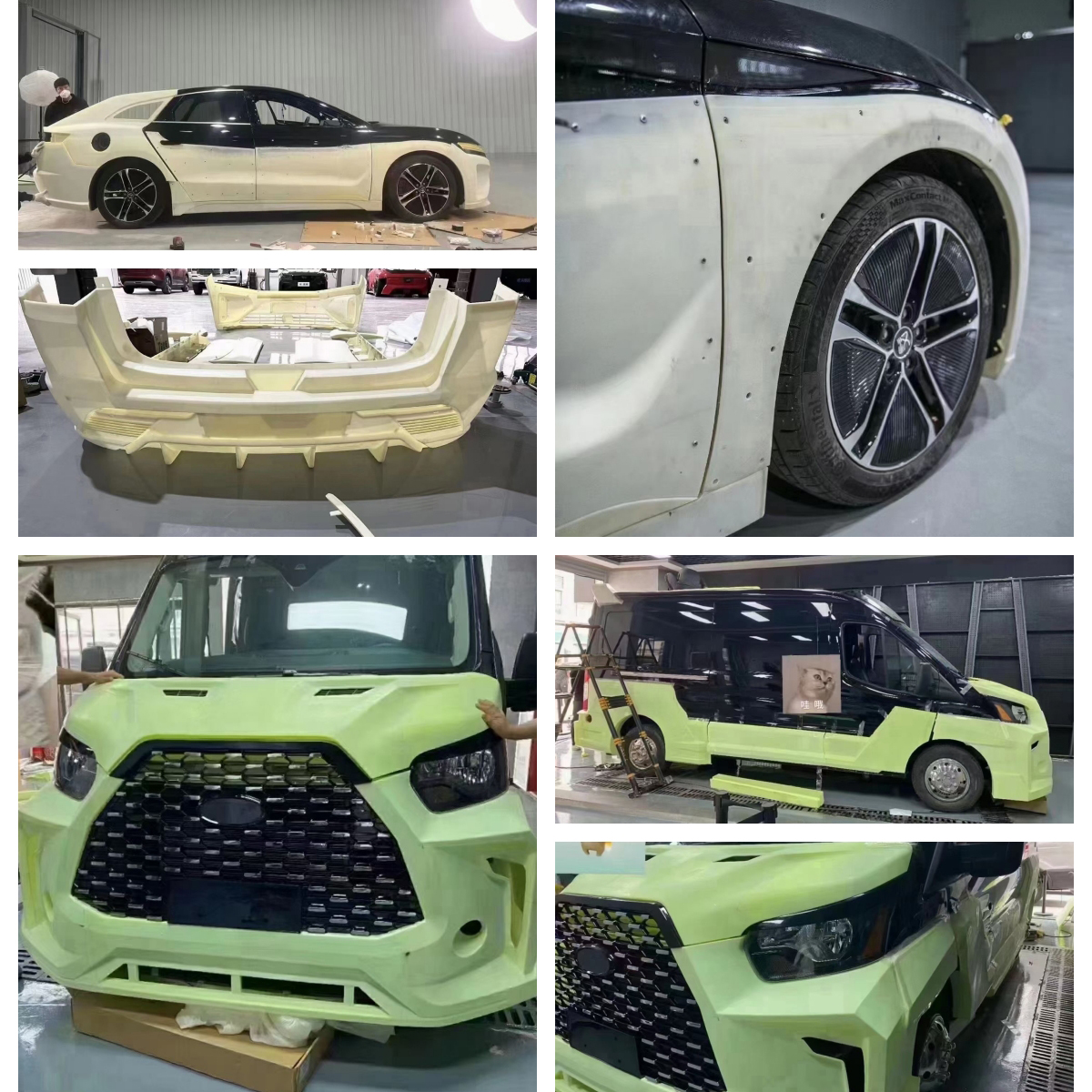
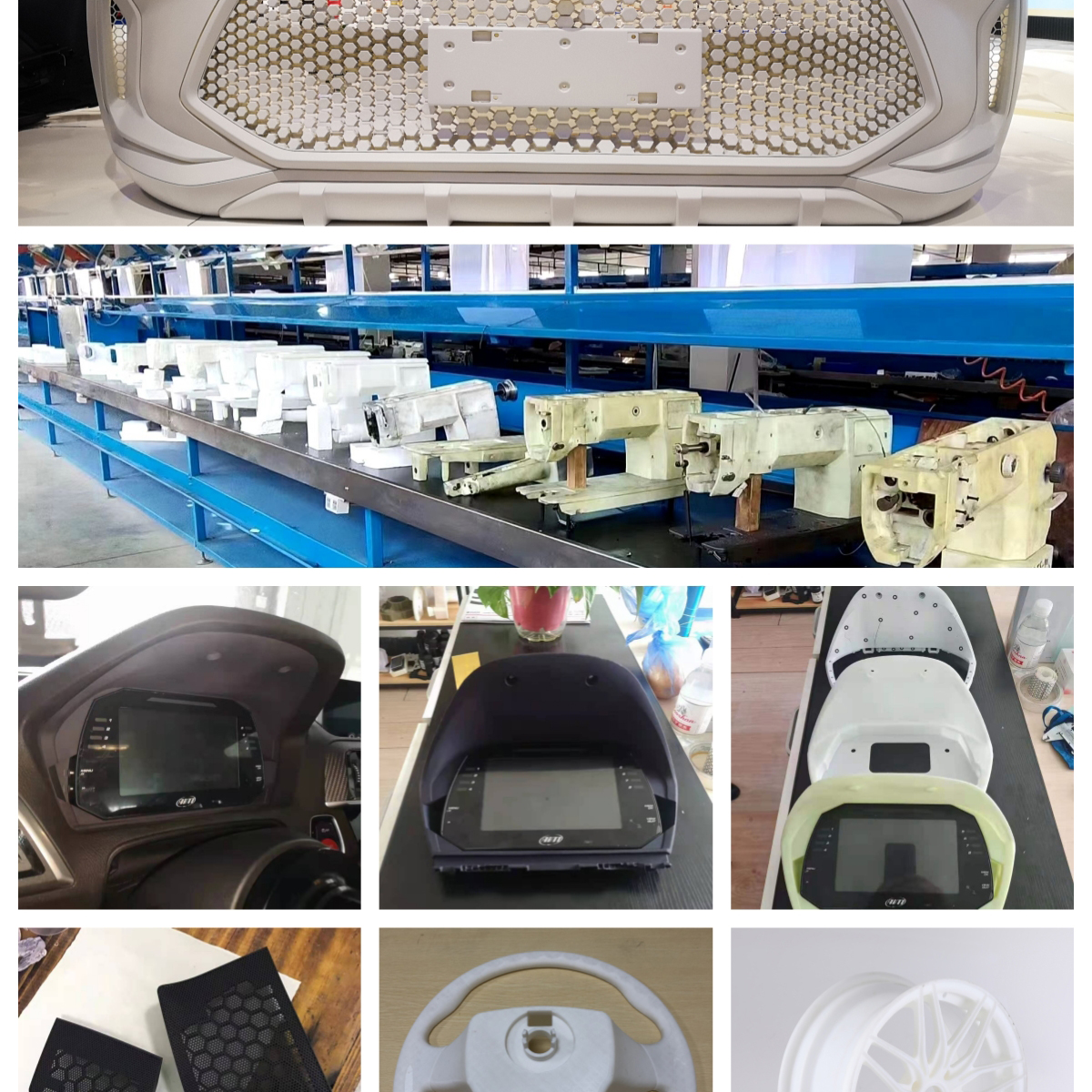
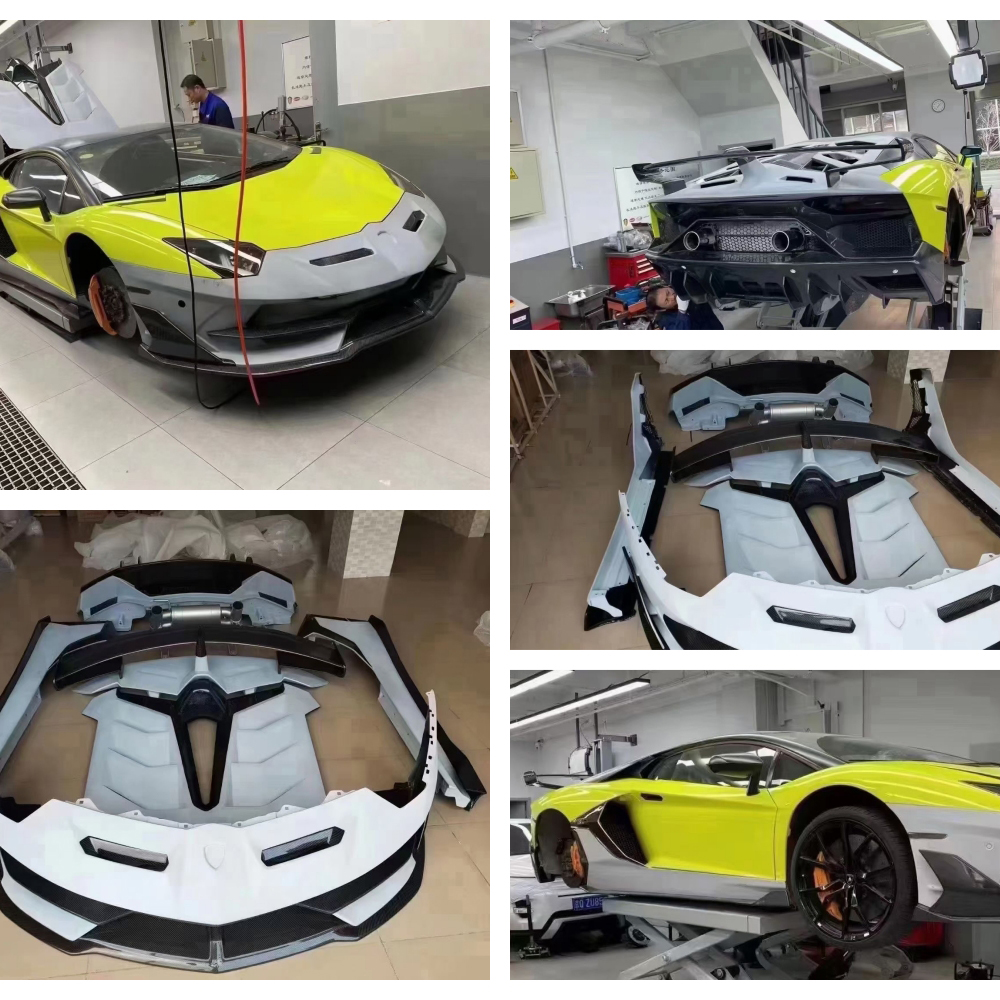
laser system | Laser type | Two-stage tube solid state laser |
wavelength | 355nm | |
power | 3000mw | |
Maximum molding space (XYZ) | 800*800*400 | |
Printing layer thickness accuracy (Quick production layer thickness) | 0.1mm-0.15mm | |
Make tight layers thick | 0.05mm-0.1mm | |
optical scanning system | Spot diameter | 0.1mm-0.12mm |
Scanning speed | 5.0m/s (Standard) 12.0m/s(maximum speed) | |
Scanning galvanometer | High speed galvanometer | |
Recoating system | Intelligent vacuum adsorption coating system | |
Accuracy of lifting system Vertical resolution | 0.0002mm | |
Repeated positioning accuracy | ±0.01mm | |
Resin cylinder capacity | 250/480/890 KG | |
software environment | Operating system | WINDOWS7/10 |
Control software | QUBEWARE PRO | |
File format | STL & SLC | |
Network compatibility | 10/100m Ethernet card access | |
operating environment | Operating temperature range | 25-30℃ |
Operating humidity range | No more than 40% | |
Machine size (W*D*H) | 1250*1310*2100 | |
Machine weight | 880KG(not including resin weight) | |
Power supply | 200~240V AC 50/60HZ,16Amps | |
Shelf life | 12 months |
- Features:
Large Print Size: Capable of printing up to 800x800x400mm, ideal for creating complex and detailed models.
High Precision: Adjustable layer thickness from 0.025-0.3mm for intricate details.
Closed Body Design: Effectively blocks harmful particles during printing, enhancing the success rate.
- Advantages:
Fast Scanning: Utilizes galvanometer scanning technology for rapid and uniform scanning.
Intelligent Operation: User-friendly interface with automated parameter settings for easy operation.
High Reliability: Precision lead screw slide table and stable electrical system ensure long-term stability.
Application of SLA resin 3D printer
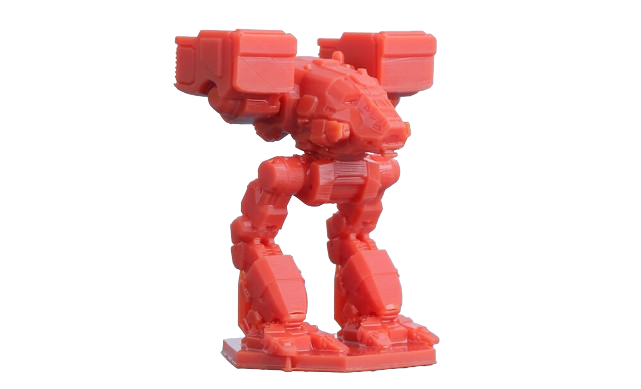
Test your part
We provide sample testing service, allowing you to check the working quality of our 3D printer before placing an order
More SLA resin 3D printers
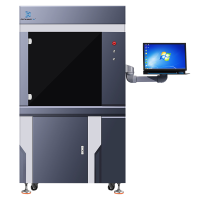
SLA-600 3D Printer
Dreambot3D SLA 3D printer offers excellent printing precision and smooth surface quality, making it easy for post-processing (0.05mm-0.1mm). This makes it a perfect choice for industrial applications.
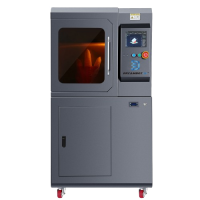
SLA-300 3D Printer
Industrial SLA 3D Printer offers modular upgrade options, supporting automatic double doors, automatic feeding, and remote monitoring, meeting the personalized customization needs of Industry 4.0.
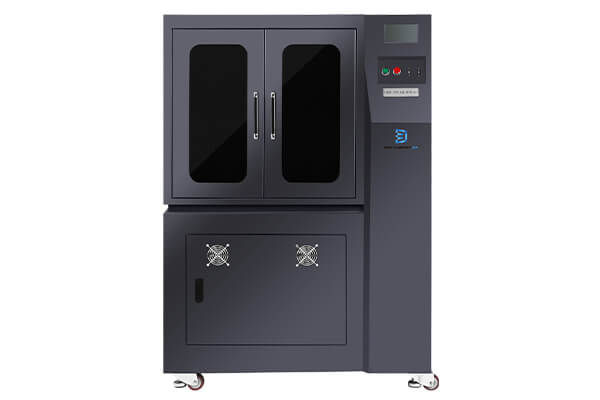
DB-550 LCD 3D Printer
The DB-550 3D printer is used to print complex objects with many angles. They are also used for large commercial printing.
Large SLA Printer buying guide
Chapter 1:
Explore SLA 3D Printers
The phrase “Explore SLA 3D Printers” invites readers or prospective clients to find out more about SLA (Stereolithography) 3D printers. It offers a thorough examination of the technology, its uses, advantages, and the reasons it could be a good match for certain sectors of the economy. Understanding how SLA varies from other 3D printing methods, like FDM, and how it performs best in creating precise, high-precision models with excellent surface finishes are some examples of the kinds of things that might be explored. The sentence lays the groundwork for understanding the benefits of SLA 3D printers in many industries.
1.1, Industries Where SLA 3D Printers Are Used
1. Aerospace
- Prototyping: SLA printers are used to create high-precision prototypes for testing aerodynamic properties and structural integrity.
- Tooling: They are employed to produce complex tooling components and molds with high accuracy.
2. Automotive
- Design Prototypes: Automakers use SLA printers to develop detailed prototypes of vehicle parts, allowing for rigorous testing and refinement.
- Custom Parts: They create customized or low-volume parts, such as specialized interior components or bespoke accessories.
3. Healthcare
- Medical Devices: SLA printers are used to produce custom prosthetics and implants, which require precise fit and functionality.
- Dental Applications: They manufacture dental models, aligners, and crowns with high accuracy.
4. Jewelry
- Casting Patterns: SLA printers create detailed wax patterns for investment casting, enabling intricate designs and fine details in jewelry pieces.
- Custom Designs: Jewelers use SLA technology for creating custom, one-of-a-kind pieces quickly.
5. Consumer Goods
- Product Prototypes: SLA printers help design and test consumer products like electronics enclosures, kitchen gadgets, and toys.
- Customization: They are used to create personalized or limited-edition items, catering to niche markets.
6. Architectural Models
- Detailed Models: Architects use SLA printers to create highly detailed and accurate scale models of buildings and urban plans.
- Client Presentations: These models help clients visualize architectural designs more clearly.
7. Education and Research
- Educational Tools: SLA printers are used to create physical models for educational purposes, including scientific and engineering demonstrations.
- Research Prototypes: Researchers utilize SLA technology for developing and testing new theories and designs.
8. Industrial Manufacturing
- Functional Prototypes: SLA printers create functional prototypes that are used in the development of manufacturing equipment and machinery.
- Tooling and Fixtures: They produce custom tooling and fixtures for industrial applications, enhancing production efficiency.
9. Art and Design
- Artistic Creations: Artists and designers use SLA printers to bring complex and intricate artistic visions to life.
- Custom Sculptures: They create custom sculptures and installations with high levels of detail.
1.2, Features of SLA 3D Printers
1. High Resolution
- Precision: SLA printers can achieve extremely high resolution, with layer thicknesses as fine as 25 microns. This allows for detailed and intricate parts with smooth surface finishes.
- Accuracy: They provide precise dimensional accuracy, making them ideal for applications requiring tight tolerances.
2. Smooth Surface Finish
- Minimal Post-Processing: Parts produced by SLA printers have smooth surfaces with minimal visible layer lines, often reducing the need for extensive post-processing.
3. Material Variety
- Resins: SLA printers use a range of photopolymer resins that can be tailored for different properties, including flexibility, rigidity, transparency, or biocompatibility.
- Specialty Resins: There are resins specifically designed for applications like casting, dental work, and high-temperature environments.
4. High Detail Capability
- Complex Geometries: SLA technology excels in producing complex and intricate geometries that may be challenging to achieve with other 3D printing methods.
- Fine Features: It can reproduce fine details and small features with high fidelity.
5. Consistent Quality
- Repeatability: SLA printers offer consistent quality across multiple prints, ensuring uniformity and reliability in production.
6. Rapid Prototyping
- Fast Turnaround: SLA technology allows for rapid production of prototypes, enabling quick iterations and testing during the design phase.
7. Support Structures
- Automatic Generation: SLA printers often feature software that automatically generates support structures, aiding in the printing of overhangs and complex shapes.
- Easy Removal: Supports are usually easy to remove after printing, leaving minimal marks on the final part.
8. Large Build Volumes
- Scalability: While SLA printers are available in various sizes, some models offer large build volumes, accommodating larger or multiple parts in a single print.
9. Controlled Environment
- Enclosed Printing Chamber: Many SLA printers have enclosed build chambers, which help maintain optimal curing conditions and improve print quality.
10. Post-Processing Requirements
- Cleaning and Curing: SLA prints typically require post-print cleaning in a solvent (such as isopropyl alcohol) and additional curing under UV light to achieve their final properties.
11. Advanced Features
- Automated Resin Handling: Some SLA printers come with automated resin handling systems, reducing manual intervention and improving workflow efficiency.
- Integrated UV Curing Stations: Certain models include integrated UV curing stations, streamlining the post-processing phase.
1.3, Why You Need an SLA 3D Printer
1. High Precision and Detail
- Accuracy: SLA printers are known for their ability to produce parts with exceptional accuracy and fine details. If your projects require intricate designs or tight tolerances, an SLA printer is a valuable asset.
- Smooth Finishes: The high resolution of SLA printing results in parts with smooth surfaces, reducing the need for extensive post-processing.
2. Rapid Prototyping
- Speed: SLA technology allows for fast turnaround times on prototypes, enabling quicker iterations and reducing development cycles.
- Efficiency: Rapid prototyping helps streamline the design process, allowing for faster validation and adjustment of concepts.
3. Complex Geometries
- Design Flexibility: SLA printers can handle complex geometries and intricate designs that might be challenging with other manufacturing methods.
- Advanced Features: They can produce detailed features and fine structures, such as lattice frameworks and internal cavities.
4. Versatile Materials
- Material Options: SLA printers offer a range of photopolymer resins with various properties, including flexibility, rigidity, transparency, and biocompatibility.
- Specialty Resins: Access to specialty resins allows for specific applications such as dental work, casting, or high-temperature environments.
5. Consistent Quality
- Reliability: SLA printers provide consistent and repeatable results, ensuring high-quality production across multiple prints.
- Uniformity: This reliability is crucial for applications requiring precise and uniform parts, such as in aerospace, automotive, or healthcare.
6. Reduced Production Costs
- Cost-Effective Prototypes: SLA printing can be more cost-effective for creating prototypes compared to traditional manufacturing methods, especially for small batches.
- Minimal Waste: The additive nature of SLA printing generates less material waste compared to subtractive manufacturing processes.
7. Customization and Personalization
- Custom Parts: SLA technology is ideal for creating customized or personalized products, whether for consumer goods, jewelry, or medical devices.
- Bespoke Designs: It enables the production of one-of-a-kind items or small runs of unique designs.
8. Educational and Research Applications
- Teaching Tool: SLA printers are useful in educational settings for demonstrating complex concepts in design and engineering.
- Research Prototypes: Researchers use SLA technology to develop and test new ideas and concepts efficiently.
9. Art and Design
- Creative Freedom: Artists and designers use SLA printers to bring creative visions to life with high precision and detail.
- Artistic Projects: They can produce custom sculptures, models, and installations that push the boundaries of traditional art.
10. Efficiency in Production
- Tooling and Fixtures: SLA printers can produce custom tooling, jigs, and fixtures, enhancing manufacturing processes and improving production efficiency.
11. Support for Innovation
- Technological Edge: Owning an SLA printer provides access to cutting-edge technology, supporting innovation and staying ahead in competitive industries.
SLA Printer vs. FDM Printer
SLA 3D Printers: Offer high precision and detail, making them ideal for applications requiring fine design and smooth surfaces (such as jewelry and dental products). They use photopolymer resins and require post-print cleaning and UV curing. While the initial and maintenance costs are higher, they excel in detail and surface quality.
FDM 3D Printers: More cost-effective, suitable for functional prototypes and larger objects. They use thermoplastic filaments, offering faster print speeds and larger build volumes but with less precision and smoothness compared to SLA. Maintenance is simpler, though post-processing may be needed.
2.1, Technology
1. Printing Mechanism
SLA (Stereolithography)
- Technology: SLA uses a laser to cure photopolymer resin layer by layer in a vat of liquid resin. The laser traces the design on the surface of the resin, solidifying it into a precise layer.
- Process: The build platform lowers into the resin, and each layer is cured before the next layer is added.
FDM (Fused Deposition Modeling)
- Technology: FDM extrudes thermoplastic filament through a heated nozzle, which melts and deposits the material layer by layer to build up the part.
- Process: The nozzle moves in horizontal and vertical directions, depositing melted filament that cools and solidifies to form each layer.
2. Resolution and Detail
SLA
- Resolution: High resolution with layer thicknesses as fine as 25 microns. Capable of producing intricate details and smooth surface finishes.
- Detail: Excellent for detailed and complex geometries.
FDM
- Resolution: Typically has larger layer heights, ranging from 50 to 300 microns. Detail and surface smoothness are generally lower compared to SLA.
- Detail: Adequate for less intricate designs and larger features.
3. Material Types
SLA
- Materials: Uses photopolymer resins, which can be tailored for various properties such as flexibility, rigidity, transparency, and biocompatibility.
- Specialty Resins: Available for specific applications like dental, casting, and high-temperature uses.
FDM
- Materials: Uses thermoplastic filaments such as PLA, ABS, PETG, and TPU. Materials are melted and extruded to build the part.
- Variety: Offers a broad range of filaments but generally less specialized compared to SLA resins.
4. Print Speed and Efficiency
SLA
- Speed: Can be slower due to the need for curing each layer with UV light. Speed may vary depending on the complexity of the print.
- Efficiency: Efficient for producing high-detail parts, though build time can be longer for complex models.
FDM
- Speed: Generally faster, especially for larger or less detailed prints. Continuous extrusion allows for quicker production.
- Efficiency: More efficient for producing larger volumes or simpler parts.
5. Support Structures
SLA
- Supports: SLA printers use support structures that are often soluble or easier to remove, reducing post-print cleanup.
- Post-Processing: Typically requires cleaning in a solvent and additional UV curing to achieve final properties.
FDM
- Supports: FDM uses support structures that are made from the same filament or specialized support filaments, which can be more labor-intensive to remove.
- Post-Processing: Often requires sanding or additional finishing to improve surface quality.
6. Cost and Maintenance
SLA
- Cost: Higher initial cost and ongoing material costs due to the price of resins.
- Maintenance: Requires careful handling of resins, cleaning of the resin tank, and occasional calibration.
FDM
- Cost: Lower initial cost and more affordable filament options.
- Maintenance: Generally easier to maintain with straightforward filament changes and occasional nozzle cleanings.
7. Build Volume
SLA
- Volume: Build volumes vary but tend to be smaller compared to some FDM printers, though large-scale SLA printers are available.
FDM
- Volume: Typically offers larger build volumes, making them suitable for bigger prints or multiple parts in one job.
2.2, Precision
1. Resolution
SLA (Stereolithography)
- Layer Thickness: SLA printers can achieve layer thicknesses as fine as 25 microns, allowing for extremely high resolution.
- Detail Accuracy: SLA provides very high detail and precision, suitable for creating intricate patterns, small features, and complex geometries.
FDM (Fused Deposition Modeling)
- Layer Thickness: FDM printers typically have layer thicknesses ranging from 50 to 300 microns. While some advanced FDM printers can achieve finer resolutions, they generally do not match the precision of SLA.
- Detail Accuracy: FDM’s precision is limited by the size of the nozzle and the nature of the filament deposition. Details and surface finishes are usually less refined compared to SLA.
2. Surface Finish
SLA
- Smoothness: Parts produced with SLA have very smooth surfaces with minimal visible layer lines, often reducing the need for post-processing.
- Detail Reproduction: SLA excels in reproducing fine surface details and features with high fidelity.
FDM
- Smoothness: FDM parts often have visible layer lines and may require additional sanding or finishing to achieve a smooth surface.
- Detail Reproduction: Surface detail can be less precise, with potential for artifacts like striations or inconsistencies in the finish.
3. Dimensional Accuracy
SLA
- Precision: SLA printers offer high dimensional accuracy, with tight tolerances and minimal deviations. This makes them suitable for applications where exact measurements are crucial.
- Consistency: SLA provides consistent results across multiple prints, maintaining high accuracy for both single and repeated prints.
FDM
- Precision: FDM printers generally offer lower dimensional accuracy compared to SLA. Factors such as filament quality, nozzle size, and print temperature can affect the precision of the final part.
- Consistency: Variability in print quality can occur due to factors like thermal expansion and nozzle wear, potentially impacting consistency.
4. Feature Resolution
SLA
- Fine Features: SLA can produce very fine features and detailed patterns, such as small text, intricate lattice structures, and complex geometric shapes.
- Complex Geometries: The technology handles complex internal geometries and delicate structures with ease.
FDM
- Feature Size: FDM may struggle with very fine features or intricate details due to the limitations of the nozzle size and material extrusion process.
- Complex Geometries: While FDM can handle reasonably complex shapes, it is less adept at producing highly detailed internal structures or delicate features.
5. Support Structures
SLA
- Supports: SLA printers often use support structures that can be easily removed or dissolved, with minimal impact on the surface finish of the part.
- Impact on Precision: The support removal process generally has a minimal effect on precision, maintaining the high detail of the final part.
FDM
- Supports: FDM printers use support structures that may leave marks or require significant post-processing to remove. Supports can affect the surface quality and precision of the part.
- Impact on Precision: Support removal can impact the precision and smoothness of the final part, especially if not carefully managed.
2.3, Materials
1. Material Types
SLA (Stereolithography)
- Resins: SLA printers use photopolymer resins that cure under UV light. These resins are available in various formulations with different properties.
- Material Properties: Resins can be tailored for specific applications, including:
- Standard Resins: For general-purpose use with good detail and surface finish.
- Flexible Resins: For parts requiring some flexibility and durability.
- Rigid Resins: For high-strength and durable parts.
- Transparent Resins: For clear or semi-transparent parts.
- Specialty Resins: Such as dental, casting, and high-temperature resins, designed for specific industries and uses.
FDM (Fused Deposition Modeling)
- Filaments: FDM printers use thermoplastic filaments, which are melted and extruded through a nozzle. Common filaments include:
- PLA (Polylactic Acid): A popular, easy-to-use filament with good detail and minimal warping. It is biodegradable and suitable for a wide range of applications.
- ABS (Acrylonitrile Butadiene Styrene): Known for its strength and impact resistance, but it can warp and emit fumes, requiring ventilation.
- PETG (Polyethylene Terephthalate Glycol): Combines the ease of printing of PLA with the strength and durability of ABS. It is resistant to moisture and chemicals.
- TPU (Thermoplastic Polyurethane): A flexible filament used for making rubber-like parts that need to be elastic and durable.
- Specialty Filaments: Including composites (e.g., carbon fiber, metal-filled), high-temperature filaments, and others for specific properties.
- Filaments: FDM printers use thermoplastic filaments, which are melted and extruded through a nozzle. Common filaments include:
2. Material Properties
SLA
- Strength and Durability: SLA resins can be engineered to achieve high strength, rigidity, or flexibility depending on the application.
- Surface Finish: SLA resins generally provide smooth surfaces and fine details, which are beneficial for aesthetic parts and precise applications.
- Post-Processing: Parts typically require post-processing to achieve their final properties, including cleaning and UV curing.
FDM
- Strength and Durability: FDM filaments vary in strength and durability. PLA is generally weaker but easy to print, while ABS and PETG offer greater strength and impact resistance.
- Surface Finish: FDM parts often have visible layer lines and may require additional finishing to achieve a smooth surface.
- Post-Processing: FDM parts may need sanding, painting, or other finishing processes to improve surface quality and aesthetics.
3. Ease of Use and Handling
SLA
- Handling: Resins can be messy and require careful handling. They are often stored in bottles and handled with gloves to avoid skin contact.
- Storage: Resins need to be stored properly, usually in a cool, dark place to avoid premature curing.
FDM
- Handling: Filaments are easier to handle and store compared to resins. They come in spools and can be used without special precautions.
- Storage: Filaments should be kept dry and away from moisture to prevent issues like clogging or poor print quality.
4. Cost
SLA
- Resin Cost: Photopolymer resins can be more expensive than standard filaments, especially for specialty or high-performance resins.
- Material Efficiency: SLA resin usage is generally efficient, but waste can occur during post-processing.
FDM
- Filament Cost: Thermoplastic filaments are generally less expensive than resins, with a wider range of cost options depending on the material and quality.
- Material Efficiency: FDM printers may produce more material waste, especially with support structures.
2.4, Used in the education industry
1. Precision and Detail-Oriented Applications
SLA (Stereolithography)
- Jewelry: Ideal for creating detailed and intricate designs with high surface quality. SLA’s fine resolution allows for precise casting molds.
- Dental and Medical Models: Used for producing high-precision dental implants, crowns, orthodontic devices, and medical research models. SLA’s accuracy is crucial for functional and anatomical details.
- Prototyping: Suitable for rapid prototyping of high-detail parts where fine features and smooth surfaces are critical. Often used in product design and development for accurate representation.
FDM (Fused Deposition Modeling)
- Functional Prototypes: Commonly used for creating functional prototypes where precise surface finish is less critical but durability and usability are important. FDM is suitable for testing form, fit, and function.
- End-Use Parts: Can produce strong and functional parts, such as housings, brackets, and tools. Though less detailed, it is sufficient for parts that will undergo further testing or modification.
- Educational Models: Used for educational purposes to demonstrate engineering principles and design concepts, where high precision is not as critical.
2. Large and Structural Parts
SLA
- Limitations: SLA printers generally have smaller build volumes, which can limit their use for larger parts. Larger parts may need to be printed in sections and assembled post-printing.
- Applications: Best suited for medium-sized parts or detailed components where high resolution is crucial, but not ideal for very large structures.
FDM
- Advantages: FDM printers often have larger build volumes, making them suitable for producing larger parts or multiple parts in a single print job.
- Applications: Ideal for creating large-scale prototypes, tooling, or parts that require significant structural integrity.
3. Complex Geometries
SLA
- Capabilities: Excellent for complex geometries, intricate details, and internal structures. SLA can produce fine lattice structures and detailed internal features without sacrificing resolution.
- Applications: Useful for parts requiring advanced design features, such as complex geometric shapes, internal cavities, or intricate patterns.
FDM
- Capabilities: Can handle moderately complex geometries but may struggle with very fine details or intricate internal structures due to limitations in nozzle size and filament deposition.
- Applications: Suitable for parts with moderate complexity, including functional prototypes and custom designs, though additional post-processing might be required for complex features.
4. Aesthetic and Artistic Applications
SLA
- Detail: Provides superior surface quality and detail, making it ideal for high-quality artistic models, collectibles, and custom designs where appearance is a primary concern.
- Applications: Used for art pieces, custom figurines, and high-fidelity models that require a smooth finish and intricate detail.
FDM
- Detail: Surface finish and detail are generally lower, making FDM less suitable for applications where visual aesthetics and fine detail are critical.
- Applications: Can be used for functional artistic pieces or larger-scale sculptures where the focus is more on form and function rather than fine detail.
5. Functional and Durable Parts
SLA
- Durability: SLA parts can be strong and durable but are generally less suited for applications requiring high impact resistance or flexibility compared to some FDM materials.
- Applications: Suitable for high-precision applications where parts will be used in controlled environments or as part of assemblies.
FDM
- Durability: FDM parts are typically more robust and can be made from materials with high impact resistance and flexibility, such as ABS and PETG.
- Applications: Ideal for functional parts, mechanical components, and prototypes that need to withstand physical stress or be used in practical applications.
Conclusion
Superior surface finishes, exquisite detail, and accuracy make SLA 3D printing technology stand out. It is the best option for applications requiring precise measurements and complex designs, such jewelry manufacturing, dentistry and medical models, and complicated prototypes. SLA printers are perfect for situations where structural accuracy and visual aesthetics are important since they can generate complex geometries with a high degree of detail and excellent resolution.
In terms of surface quality and detail, SLA has more benefits than disadvantages, even with increased material costs and the need for post-processing. SLA is the best technology for applications needing the most intricate details, flawless finishes, and intricate structures. It is the go-to option in sectors where accuracy is crucial due to its capacity to handle delicate characteristics and provide excellent outcomes.
In summary, SLA 3D printing technique is the best option if your project demands outstanding detail, surface polish, and accuracy. It is perfect for situations where attention to detail is crucial since it provides unparalleled quality and accuracy.