Structured Light 3D Scanner
- With 6.3 Million PM
- 0.01mm Precision ≤ 3s Fast Scanning
- 0 Radiation Safe Scanning, Compatible With Multiple File Formats
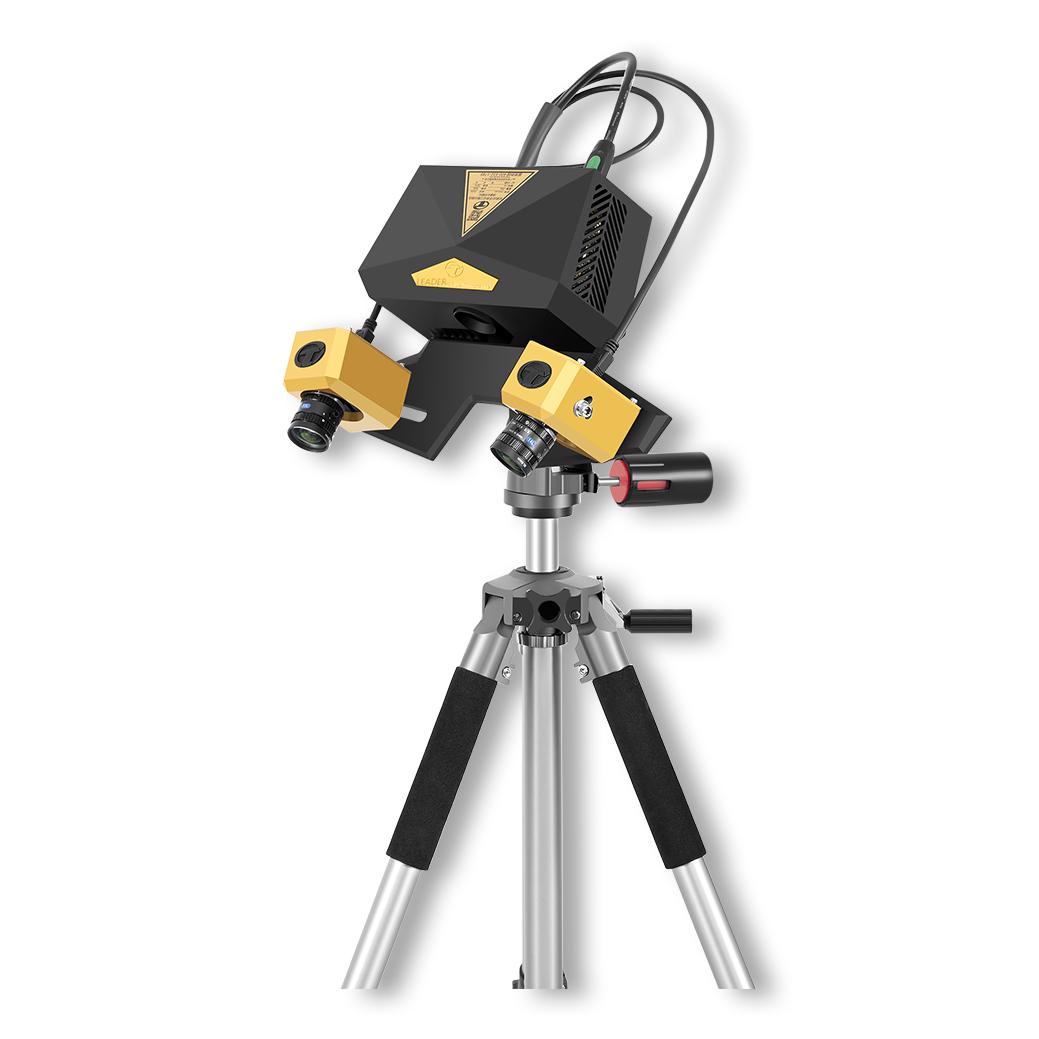
Blue Light 3D Scanner
A wide range of industries and applications that demand precise and thorough 3D data about item geometry rely heavily on structured light 3D scanners. These scanners, such as the popular “blue light 3D scanner,” offer numerous benefits in various areas.
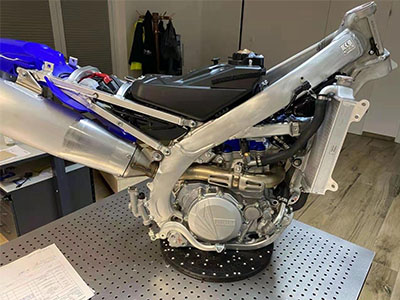
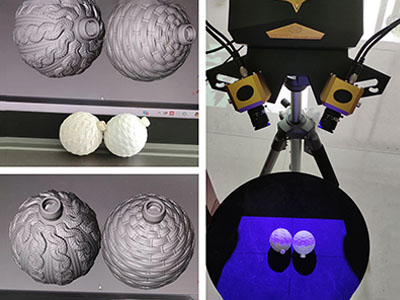
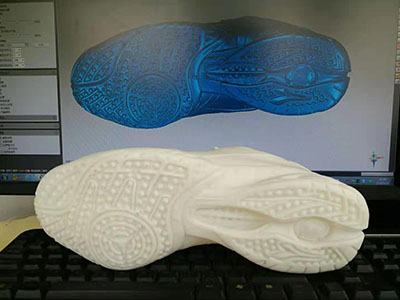
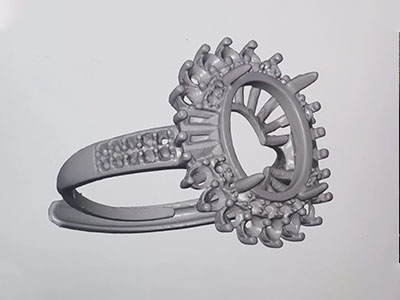
- Structured light 3D scanners are made to accept a wide range of things, from little goods like jewelry and electrical components to enormous objects like equipment, automobiles, and even skyscrapers. Because of their adaptability, they may be used in a broad variety of sectors.
- Structured light 3D scanners employ a radiation-free, non-contact scanning technique that uses no radiation at all. This makes them perfect for scanning fragile things as well as those that could be risky or difficult to scan using conventional techniques.
- Data acquired from a structured light 3D scanner is easily convertible to several file formats, making it compatible with a variety of software programs.
- The lens used in structured light 3D scanners is of excellent quality, delivering a crisp and exact image of the object being scanned. It is imported from Japan and has a resolution of 6.3 megapixels. This makes it easier to guarantee the accuracy and high quality of the final 3D model.
- Blue light scanning technology: A sort of structured light scanning, blue light scanning technology makes use of blue light to take high-quality 3D pictures. This technology is renowned for having great precision and resolution, making a wide range of applications possible.
- Direct export to 3D printing files is possible for the 3D models produced by structured light 3D scanners, making it simple to produce actual items from the scanned data.
- Structured light 3D scanners employ sophisticated algorithms to automatically stitch together the scanned data, negating the need for human alignment or marking of scanning spots. Time is saved, and the final 3D model is more accurate as a result.
- High precision master data: Because structured light 3D scanners are capable of capturing data with such high accuracy, they are perfect for applications that call for precise measurements and fine details. For a variety of tasks, including quality assurance, product development, and reverse engineering, the generated 3D model can be utilized as master data.
Product model | G5-630 |
Scan Pixels: | 6.3 million2 |
Cameralens: | Japanese computar12mm |
Scanning Method: | Non contact surface scanning |
Sensor: | Hik (gray point50s5m-c) |
Camera Lens: | Lens(Computar 8mm, Japan) |
Single Measurement Format: | 400*300,300*225,200*150,100*75,5035mm |
Single Amplitude Measurementaccuracy: | ≤±0.01mm;≤0.025mm/600mm |
Singlemeasurement Time: | ≤3s |
Measuring Point Distance: | 0.05~0.40mm |
Grating Technology: | Extrapolation multi frequency phase shift gratingtechnology |
Calibration Technology: | Checkerboard calibration technology |
Scanninghead Size: | 300*200*100mm |
Splicing Method: | Full automatic splicing and non sticking scanning of marker points |
Developer: | Exceptfor transparent,translucent and highly reflective parts, there is no need to spraydeveloper |
Operating System: | Windows 7 64 bit |
Ratedvoltage And Frequency: | 100-240V,50~60Hz |
Rated Current: | Rated current 3.5A |
Operating Temperature: | 7-50°C(50-104°F) |
Humidity Range: | Relative humidity 65% or lower, no dew |
Allow Ambient Light: | Office environment |
Safetyinstructions: | Professional blue light system is adopted, which has strong anti-interference of ambient lightand isharmless to human body |
Application Scenarios For Structured Light 3d Printing
3D Scanner For Car Parts
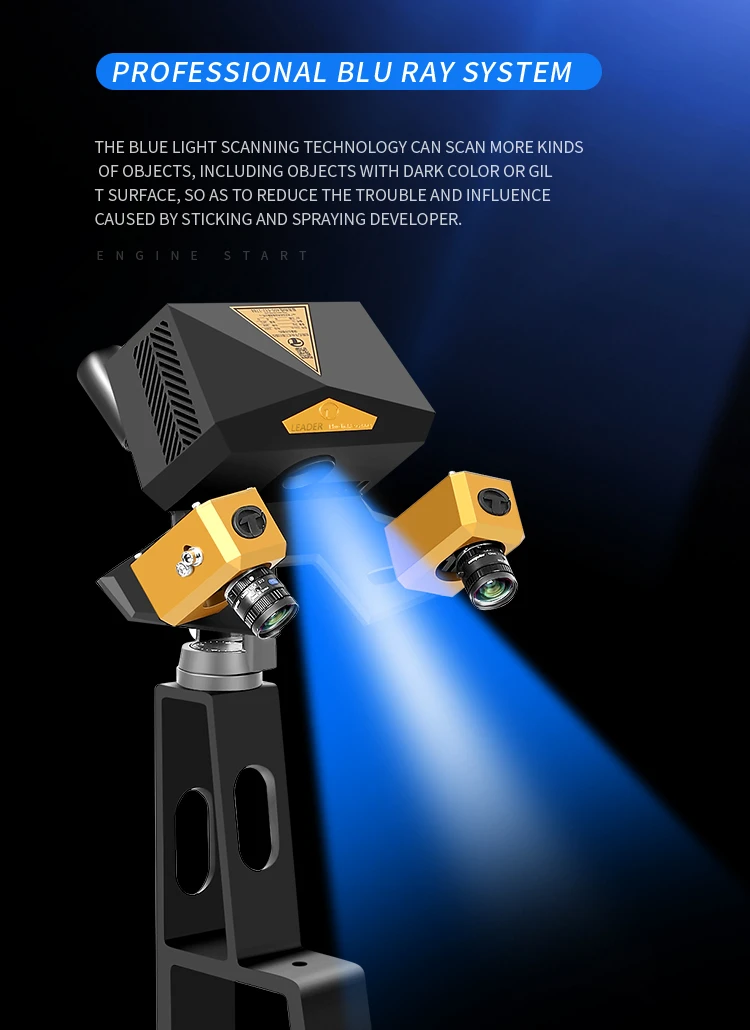
- Accurate scanning: 3D scanners can accurately record the shape and dimensions of automotive components, resulting in 3D models that are as accurate as possible.
- Versatility: From little bits to whole automobile bodies, 3D scanners can scan a variety of automotive components. A single scanner may be utilized for a variety of automotive applications because to its adaptability.
- Non-contact scanning: As 3D scanners don’t make direct touch with the objects being scanned, there is no chance of the objects being harmed during the scanning process.
- Safe scanning: 3D scanners are a safer alternative for scanning auto components since they do not employ radiation, in contrast to conventional scanning techniques that do.
- Time-saving: Using a 3D scanner to scan automotive components is far faster than using conventional techniques, allowing you to move design and production forward more quickly.
- File format conversion enables the usage of 3D models in a range of software applications. 3D scanners are able to convert scanned data into a number of different file formats.
- High-quality lens: A 3D scanner with a high-quality lens can capture even the tiniest details of automobile components, producing 3D models that are more precise and detailed.
- Automatic stitching: Without the requirement for human scanning point alignment, certain 3D scanners can automatically combine several scans of an automobile part to create a comprehensive and accurate 3D model.
3D Scans of Sculptures
- certain light One technique that may be used to scan sculptures is 3D scanning. With this technique, a projector is used to project a number of structured light patterns onto the sculpture, and a camera is used to concurrently take pictures of the patterns. On the sculpture’s surface, the patterns produce a number of lines and shapes that are utilized to build a 3D point cloud.
- The sculpture’s digital model is created once the point cloud has been analyzed. In order to create a comprehensive 3D model, it is necessary to use software to align and combine the many point clouds that were collected from various perspectives. A high-quality digital reproduction of the original sculpture may be created by editing and perfecting the resultant model.
- Structured light scanning is a non-contact technique, making it especially beneficial for delicate or fragile sculptures because the sculpture is not touched during the scanning process. Due to the scanner’s ability to record very minute details and complex characteristics, it also permits extremely high levels of accuracy. In general, structured light 3D scanning is a useful and practical technique for creating high-quality digital sculpting models.
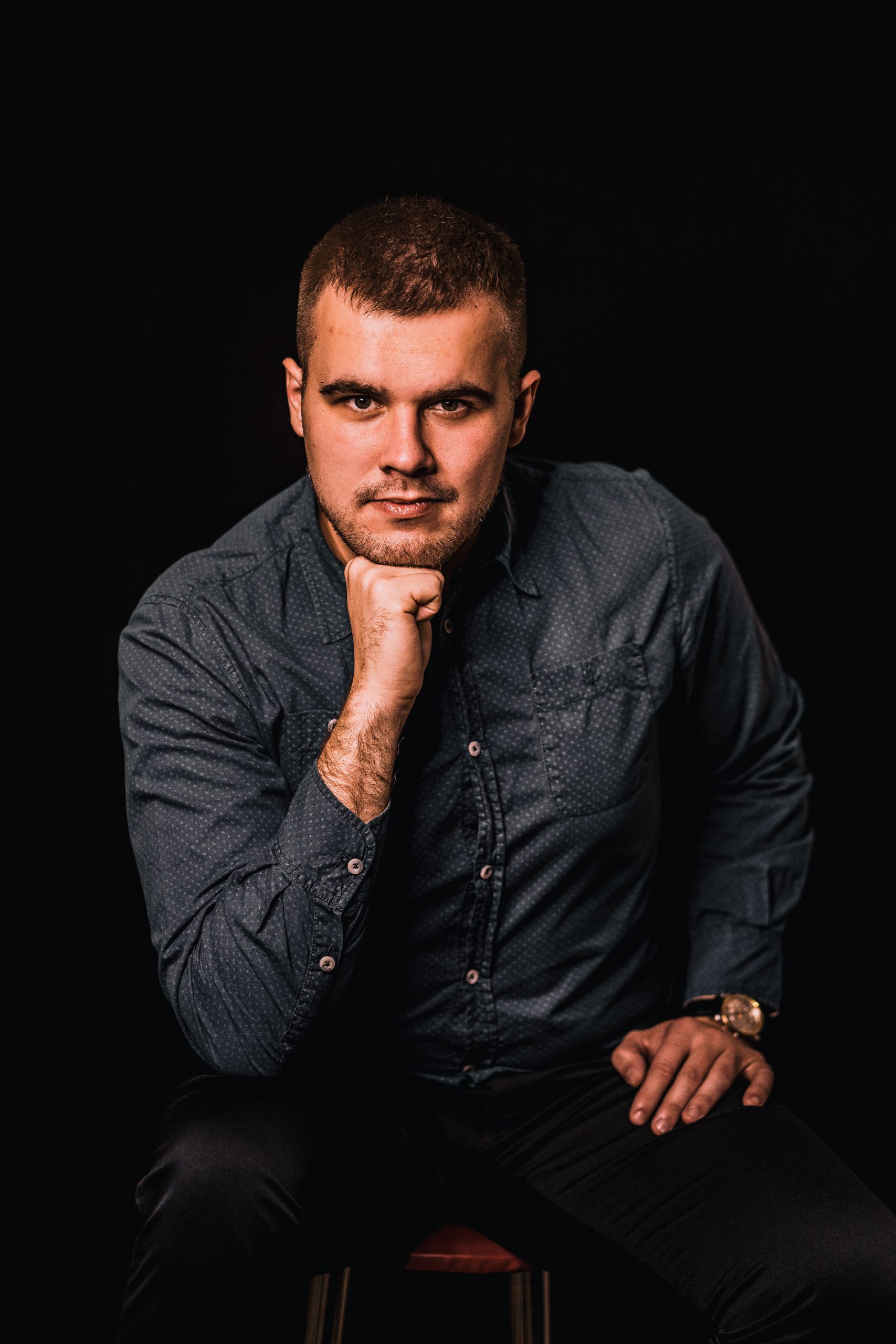
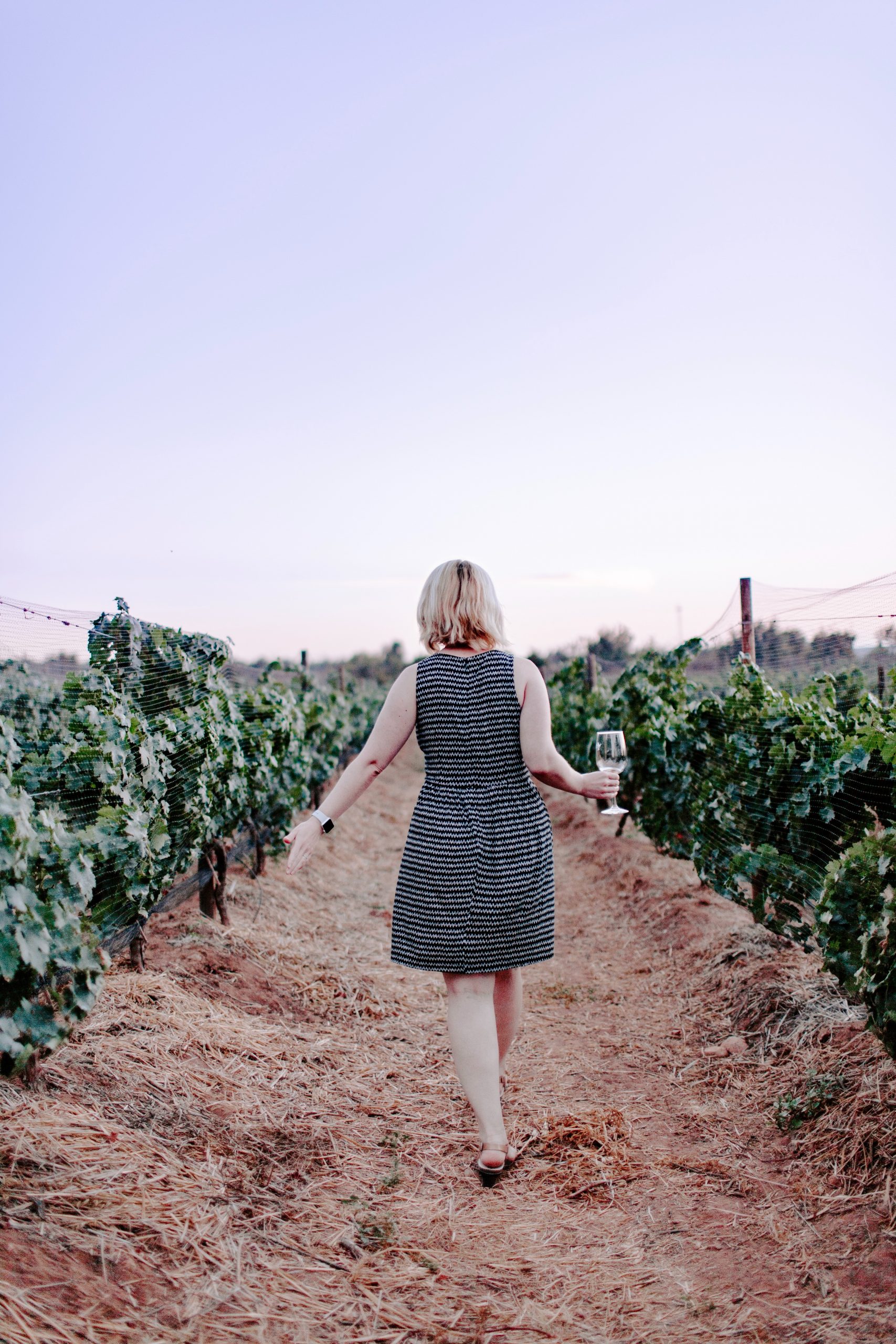
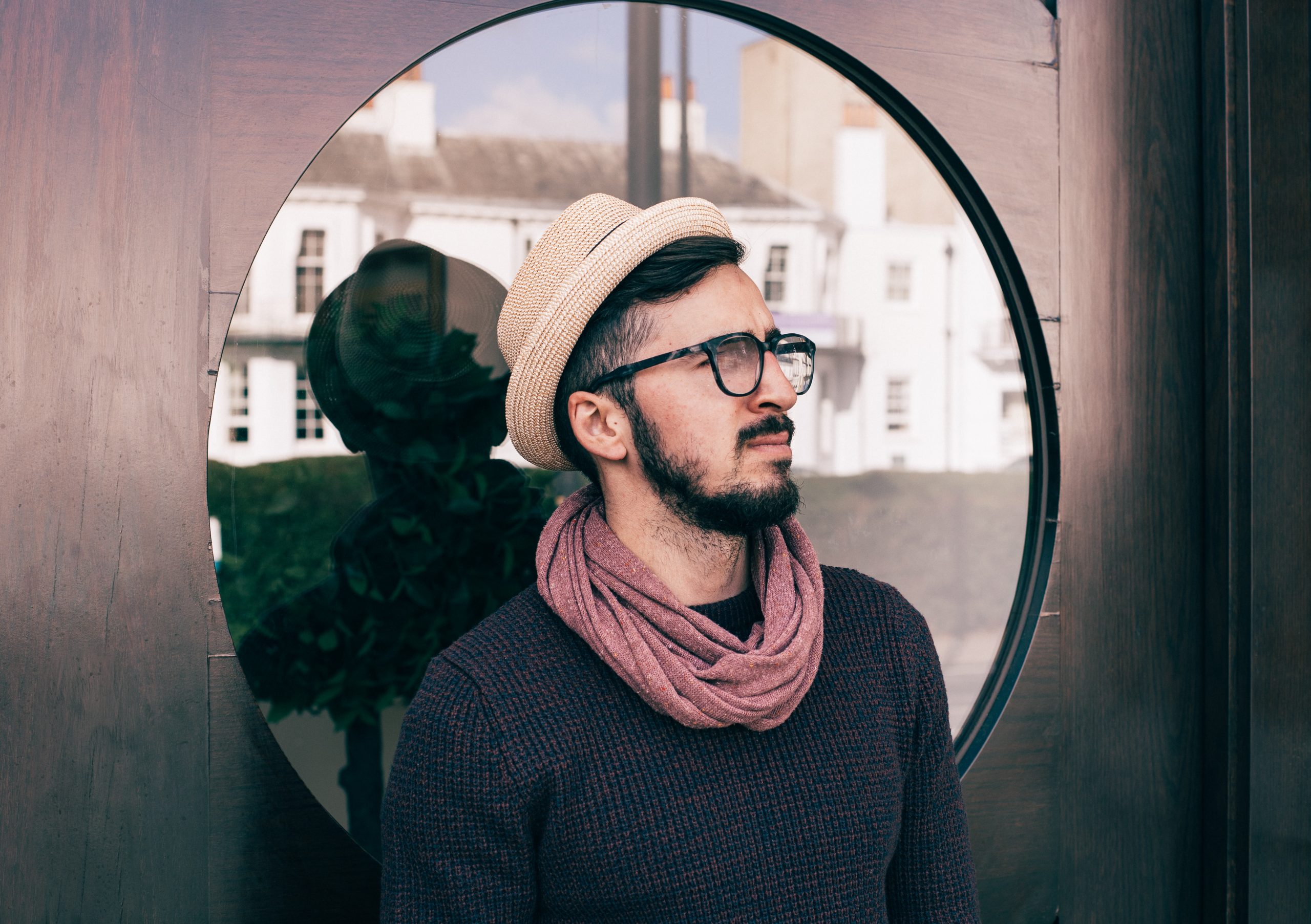
Contact Us
industrial 3d printer manufacturers
Dreambot 3D scanners assist you in scanning the structure of any object with high precision and accurate data.
3D scanners play a crucial role across various industries, helping businesses increase efficiency, reduce costs, and optimize products and services.
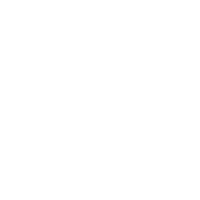
CE FCC ROSH approved
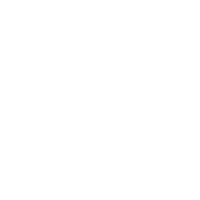
Solution for 3d printing
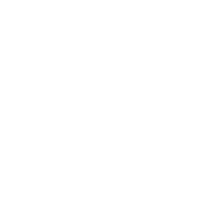
High quality
FDM 3D printers for your choice
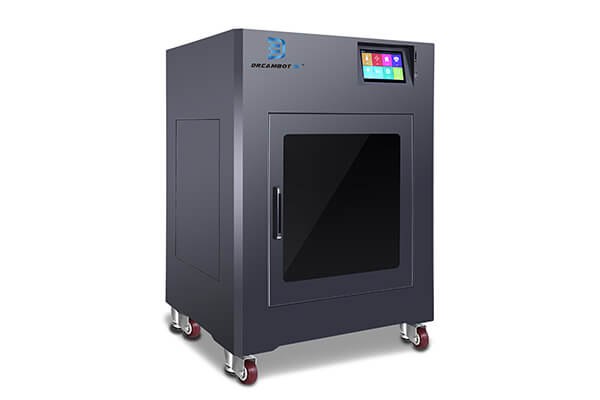
L-300 FDM 3D Printer
The L-300 printer has a dimension of 300*300*300mm, suitable for personalized or small scale printing. It has a stable frame for printing accuracy.
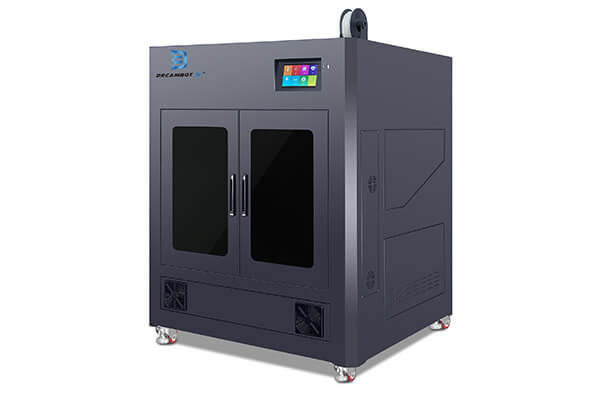
L-800 FDM 3D Printer
The L-800 is suitable for industrial printing applications. The printing diameter is 800*800*800mm for accurate and detailed printing.
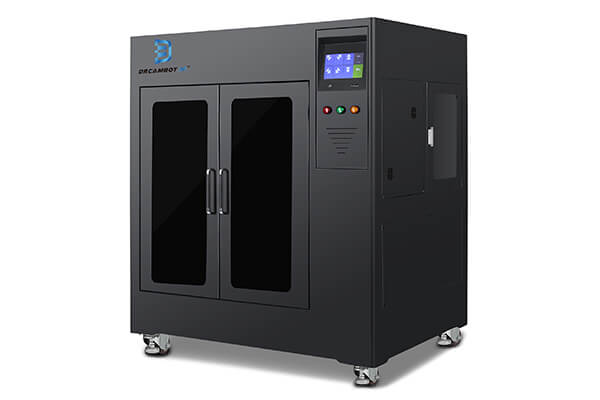
L-1000 FDM 3D Printer
The L-1000 printer is an industrial printer used for large scale printing. Its printing dimension is 1000*1000*1000mm and a precision of 0.05mm.
FAQ About Structured Light 3D Scanner
Blu-ray scanning, commonly referred to as blue light scanning, is a 3D scanning method that takes incredibly precise and detailed 3D representations of items using blue light. The following are the key advantages of blue light scanning:
High precision: Because blue light has a shorter wavelength than other forms of light used in 3D scanning, it can capture the geometry and surface features of objects with more accuracy.
Rapid data capture is made possible by the employment of quicker cameras and projectors in blue light scanning technology.
Safe for sensitive materials: Blue light is a great alternative for scanning goods that may be harmed by other scanning techniques since it is non-damaging to delicate materials like human skin or biological products.
Blue light scanning is a versatile alternative for a number of industries and applications since it can be utilized on a broad variety of objects, including highly shiny surfaces.
Overall, blue light scanning is becoming a more common option in sectors including manufacturing, engineering, and healthcare since it provides extremely precise and effective 3D scanning capabilities.
A sort of 3D scanning technology called blue light scanning use blue light to take incredibly precise 3D measurements of an object’s surface. A blue light from the scanner is directed towards the item, and a camera subsequently captures the light’s reflection. The scanner can produce a 3D representation of the item that is extremely detailed by examining the distortion of the reflected light. When accuracy is crucial, this technique is frequently employed in manufacturing, reverse engineering, and quality control applications. Blue light scanning is quicker, safer, and capable of capturing more precise and comprehensive data than other 3D scanning techniques.
Onto the item being scanned, the structured-light 3D scanner projects a pattern of light. Usually, this pattern consists of a grid of dots or a sequence of horizontal or vertical lines. Pattern capture: After being projected onto the item, the light pattern bounces back onto the scanner’s camera. The pattern is captured by the camera, which also documents any distortions and deviations brought on by the surface contour of the item. Data processing: The scanner software analyzes the pattern and determines the separation between the item and the scanner at each place on the surface. The scanner can generate a 3D point cloud of the object’s surface by adding these distance readings.
The point cloud is then used to build a mesh, or a collection of triangle-shaped faces, that roughly approximates the object’s surface. For additional use, this mesh may be exported to 3D modeling programs or 3D printers.
The shape and geometry of an object may be quickly, precisely, and in great detail utilizing structured-light 3D scanning without harming the thing. It is frequently utilized in industries including engineering, production, quality assurance, and archaeology.
certain light Both 3D scanning and 3D scanning are techniques for digitally recording an object’s shape and measurements. The two approaches do differ in several significant ways, though:
Technology: 3D scanning can be done with a laser, photogrammetry, or time-of-flight cameras. Structured light 3D scanning employs a projector and a camera to record data.
Accuracy: For small to medium-sized items, structured light 3D scanning often yields findings with better accuracy than other 3D scanning techniques.
Speed: Because structured light 3D scanning can collect data in a single scan, it is typically faster than other techniques.
Technology: 3D scanning can be done with a laser, photogrammetry, or time-of-flight cameras. Structured light 3D scanning employs a projector and a camera to record data.
Accuracy: For small to medium-sized items, structured light 3D scanning often yields findings with better accuracy than other 3D scanning techniques.
Speed: Because structured light 3D scanning can collect data in a single scan, it is typically faster than other techniques.